Slipways wiki technology offers a dynamic platform to explore the multifaceted world of slipway design, construction, operation, and maintenance. This guide delves into the historical evolution of slipways, examining various types, materials, and engineering principles. We’ll also explore modern innovations, environmental considerations, and the crucial role of safety regulations in ensuring efficient and sustainable slipway operations.
From the fundamental definitions of slipways and their diverse applications to the latest advancements in automation and sustainable practices, we aim to provide a thorough understanding of this critical maritime infrastructure. This exploration encompasses design considerations for different vessel types, detailed operational procedures, and a comprehensive cost analysis, ensuring readers gain a holistic perspective on slipway technology.
Slipway Definitions and Types: Slipways Wiki Technology
A slipway is a structure designed to facilitate the launching and hauling out of boats and other watercraft. Essentially, it’s an inclined plane, often made of concrete or timber, leading from the water’s edge to a higher ground level. This allows vessels to be moved easily between the water and dry land for maintenance, repair, or storage. Slipways vary considerably in size and complexity, ranging from simple, manually operated structures to sophisticated, mechanized systems capable of handling large ships.
Slipways are crucial for the maritime industry, providing a cost-effective and efficient method for accessing vessels for various purposes. Their design and functionality are heavily influenced by factors such as the size and type of vessels they accommodate, the tidal range of the location, and the available resources.
Slipway Types
Slipways can be categorized in several ways, primarily based on their construction and operation. The most common distinction is between gravity slipways and hauled slipways. Gravity slipways rely on gravity to move the vessel down the incline, while hauled slipways utilize a system of winches and cables to both launch and haul out vessels. Further sub-categories exist within these broad classifications, depending on the specific mechanisms and materials used. For example, some gravity slipways incorporate a cradle or wheeled carriage to support the vessel during launching, while hauled slipways may employ different types of winches and cable systems depending on the size and weight of the vessel. Variations also exist in the orientation of the slipway; some are built at a fixed angle, while others are adjustable to accommodate different tidal levels.
Slipway Construction Materials
The choice of material for slipway construction significantly impacts its durability, lifespan, and cost. Common materials include concrete, timber, and steel. Concrete slipways offer high strength and durability, making them suitable for heavy-duty applications. However, concrete can be expensive and time-consuming to construct, and it may require specialized expertise for proper installation. Timber slipways, while less durable than concrete, are often easier and cheaper to construct, especially for smaller-scale applications. However, timber requires regular maintenance to prevent rot and deterioration. Steel slipways are used less frequently due to their higher cost and susceptibility to corrosion, but they can be very strong and suitable for specific applications where their high strength-to-weight ratio is advantageous. The selection of the best material depends on the specific requirements of the project, considering factors such as budget, vessel size, and environmental conditions.
Historical Evolution of Slipway Technology
The use of inclined planes for launching and hauling out vessels dates back centuries. Early slipways were simple wooden structures, often relying on manual labor and gravity. As shipbuilding technology advanced and vessels became larger and heavier, so too did the complexity of slipway design. The introduction of winches and other mechanical devices in the 18th and 19th centuries significantly improved the efficiency and safety of slipway operations. The development of reinforced concrete in the 20th century revolutionized slipway construction, allowing for the creation of larger, more durable structures capable of handling increasingly larger vessels. Modern slipways often incorporate sophisticated control systems and safety features, reflecting advancements in engineering and materials science. Significant milestones include the adoption of steel and reinforced concrete, the development of sophisticated winch and cable systems, and the integration of computer-aided design and construction techniques.
Slipway Design and Engineering
Slipway design and engineering is a complex field requiring a thorough understanding of structural mechanics, marine engineering, and site-specific conditions. Successful slipway design ensures safe and efficient launching and hauling of vessels, minimizing risks to both the vessel and personnel. The process involves careful consideration of various factors, from the type and size of vessels to be serviced to the soil conditions of the site.
Slipway design necessitates detailed calculations to ensure structural integrity under various loading conditions. Material selection is crucial, balancing cost-effectiveness with durability and resistance to corrosion in a harsh marine environment.
Slipway System Design for a Fishing Trawler
This section details the design of a slipway system suitable for a 20-meter fishing trawler, weighing approximately 50 tonnes. The slipway will be a gravity-type system, utilizing a concrete cradle and inclined track. The design considers the vessel’s weight, dimensions, and anticipated loading during launching and hauling.
The structural calculations involve determining the required strength of the concrete cradle and the inclined track to withstand the vessel’s weight and the forces generated during movement. This includes considering factors like shear stress, bending moment, and compressive stress. The calculations are performed using standard engineering formulas and software, accounting for safety factors to ensure a significant margin of safety. For example, the concrete mix design will be specified to achieve a compressive strength exceeding 30 MPa to withstand the anticipated loads. The steel reinforcement within the concrete will be meticulously calculated to handle tensile stresses. The cradle’s design will include strategically placed supports to evenly distribute the vessel’s weight. The inclined track will be designed with a sufficient gradient to ensure smooth movement, while the surface will be textured to provide adequate friction to prevent slippage.
Comparison of Slipway Designs
Several slipway designs exist, each with its advantages and disadvantages depending on vessel size and type. Gravity slipways, as described above, are suitable for smaller vessels, offering simplicity and relatively low construction costs. They rely on gravity for launching and hauling, typically using a winch system for controlled movement. However, they are limited in their capacity and may not be suitable for very large or heavy vessels.
Alternatively, wheeled slipways utilize a system of wheeled carriages to move the vessel along the inclined track. These systems can handle larger and heavier vessels than gravity slipways, offering greater flexibility. They typically incorporate a more complex system of winches and power units for controlled movement. The increased complexity translates to higher initial costs but can lead to greater efficiency in the long run for high-volume operations.
Floating slipways, which are essentially floating docks with an inclined ramp, provide another option, particularly useful in locations with limited space or varying water levels. They are often more expensive to construct and maintain than fixed slipways but offer significant advantages in terms of versatility and accessibility.
The choice of slipway design depends on factors such as vessel size and type, budget, site conditions, and the frequency of use. A detailed feasibility study is essential to determine the most suitable design for a particular application.
Key Engineering Principles in Slipway Construction
Safety and efficiency are paramount in slipway construction. Key engineering principles include:
Proper site selection and geotechnical investigation: Ensuring stable ground conditions is crucial for structural stability.
Accurate load calculations and structural design: Accounting for all forces acting on the slipway, including the vessel’s weight, buoyancy, and dynamic forces during movement.
Material selection and corrosion protection: Choosing durable materials resistant to the harsh marine environment and implementing appropriate corrosion protection measures.
Robust construction techniques and quality control: Adhering to strict construction standards to ensure structural integrity and longevity.
Effective drainage and water management: Preventing water accumulation on the slipway to avoid structural damage and safety hazards.
Safe operating procedures and maintenance: Establishing clear guidelines for slipway operation and implementing a regular maintenance program.
Slipway Operation and Maintenance
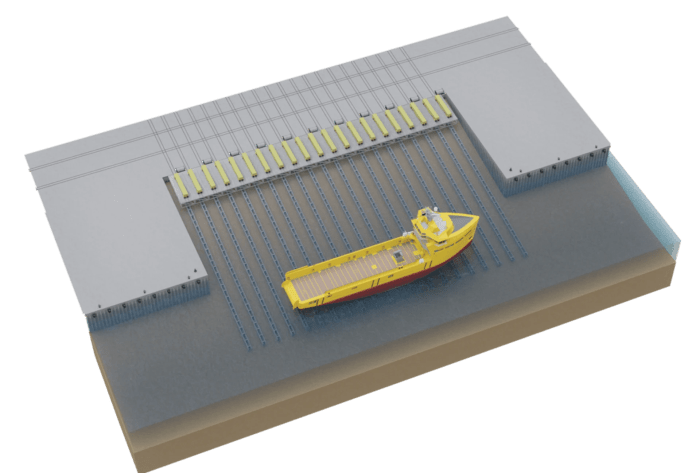
Safe and efficient slipway operation requires a well-defined procedure for launching and hauling vessels, coupled with a robust maintenance program. Ignoring either aspect can lead to costly repairs, damage to vessels, and potential safety hazards. This section details best practices for both.
Safe Launching and Hauling Procedures
A systematic approach to launching and hauling vessels minimizes risk and ensures the longevity of the slipway. The specific steps will vary depending on the slipway type and vessel size, but the underlying principles remain consistent. Before commencing any operation, a thorough pre-launch/haul inspection is crucial.
- Pre-launch/Haul Inspection: This involves checking the slipway’s structural integrity, including the cradle, tracks, winch, and braking systems. Verify the functionality of all safety mechanisms, such as emergency stops and locking devices. Inspect the vessel’s hull for any damage that could compromise its safe movement. Ensure adequate staffing for the operation, with clearly assigned roles and responsibilities.
- Securing the Vessel: The vessel should be securely cradled and properly chocked to prevent movement during the launch/haul process. Appropriate lifting points should be used, and the vessel’s weight distribution should be considered to prevent stress on the slipway structure. All loose items on the vessel should be secured to avoid damage or injury.
- Controlled Movement: The launch/haul operation should be conducted slowly and under controlled conditions. The winch operator should maintain constant communication with the ground crew to ensure smooth movement. Regular checks should be made on the condition of the cradle and tracks throughout the operation.
- Final Positioning: Once the vessel is launched or hauled, it should be secured in its final position to prevent unintended movement. This may involve using additional lines, fenders, or other securing devices. A post-launch/haul inspection should be conducted to ensure that everything is in place and that no damage occurred during the operation.
Routine Maintenance Tasks
Regular maintenance is paramount for ensuring the continued safe and efficient operation of a slipway. A preventative maintenance schedule should be implemented and meticulously followed.
- Regular Inspections: Visual inspections should be conducted at least monthly, checking for signs of wear and tear, corrosion, or damage to the slipway structure, tracks, and machinery. More thorough inspections, including structural assessments, should be conducted annually or as needed.
- Lubrication: Moving parts, such as winches, rollers, and tracks, require regular lubrication to reduce friction and prevent wear. The type and frequency of lubrication will depend on the specific components and environmental conditions.
- Corrosion Control: Slipways are often exposed to harsh environmental conditions, making them susceptible to corrosion. Regular cleaning and application of protective coatings can help extend the lifespan of the structure. Cathodic protection may be necessary in particularly corrosive environments.
- Repair and Replacement: Damaged or worn components should be repaired or replaced promptly to prevent further damage and ensure the continued safe operation of the slipway. A spare parts inventory should be maintained to minimize downtime in case of unexpected repairs.
Common Operational Problems and Solutions
Several issues can arise during slipway operation, requiring prompt attention and effective solutions.
- Winch Malfunctions: Winch failures can halt operations and potentially damage the vessel or slipway. Regular maintenance, including lubrication and inspection, can help prevent these failures. Having a backup winch or contingency plan is also advisable.
- Track Damage: Damage to the slipway tracks can lead to uneven movement and potentially derail the vessel. Regular inspections and prompt repairs are essential to prevent this. Using appropriate materials and construction techniques during the initial slipway design is also crucial.
- Cradle Issues: Cradle failures can result in vessel damage or injury. Regular inspections, proper securing of the vessel, and using cradles designed for the specific vessel type are vital. Regular checks for wear and tear on the cradle components should be part of the maintenance schedule.
- Environmental Factors: Extreme weather conditions, such as high winds or heavy rain, can impact slipway operations. Operations should be suspended during such conditions, and appropriate safety measures should be implemented to protect the slipway and the vessel.
Slipway Technology and Innovation
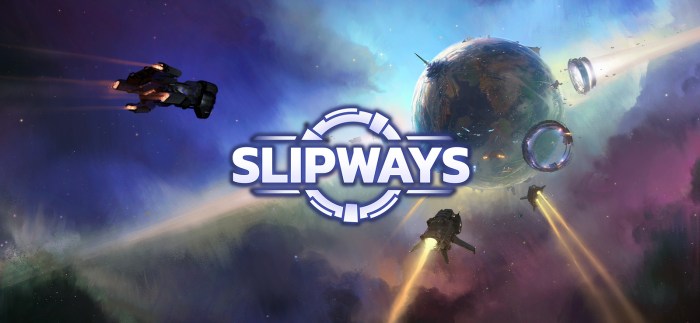
The evolution of slipway technology reflects advancements in engineering, materials science, and automation. Traditional methods, while effective, often present limitations in efficiency, safety, and environmental impact. Modern innovations aim to address these challenges, leading to more streamlined, safer, and environmentally responsible slipway operations.
Recent advancements have significantly improved slipway efficiency and safety. The integration of computer-aided design (CAD) and computer-aided manufacturing (CAM) in the design and construction phases allows for precise engineering, reducing material waste and construction time. Furthermore, the use of advanced materials, such as high-strength steels and composites, enhances the durability and lifespan of slipways, minimizing maintenance requirements.
Automated Slipway Systems
Automation is transforming slipway operations. Automated winch systems, controlled by sophisticated software, precisely manage the movement of vessels, reducing the risk of human error and improving overall efficiency. These systems often incorporate sensors and feedback mechanisms to monitor the vessel’s position and speed, ensuring a smooth and controlled launching or hauling process. For example, a fully automated system might employ laser-guided positioning for precise alignment and integrated load monitoring to prevent overloading. This results in faster turnaround times and reduced labor costs.
Comparison of Traditional and Modern Slipway Methods
Traditional slipways, often relying on gravity and manual labor, are labor-intensive and prone to delays caused by weather conditions or equipment malfunctions. Modern technologies, in contrast, offer significant improvements. Automated systems enhance speed and precision, reducing the reliance on manual labor and minimizing the impact of environmental factors. For instance, a modern automated slipway might complete a launching operation in a fraction of the time required by a traditional system, leading to significant cost savings through reduced labor costs and increased vessel turnaround. The use of advanced materials also extends the operational lifespan of the slipway, further reducing long-term costs associated with repairs and replacements.
Technology’s Role in Improving Slipway Safety and Environmental Impact
Technological advancements significantly enhance slipway safety. Automated systems reduce human error, a major cause of accidents. Integrated safety features, such as emergency stops and load monitoring, minimize the risk of vessel damage or injury to personnel. Furthermore, the use of environmentally friendly materials and practices reduces the slipway’s ecological footprint. For example, the implementation of closed-loop lubrication systems minimizes oil spills, while the use of recycled materials in construction reduces waste. The incorporation of noise reduction technologies also mitigates the environmental impact of slipway operations. These combined improvements create a safer and more sustainable operating environment.
Slipway Environmental Considerations
Slipway construction and operation can significantly impact the surrounding environment. Understanding and mitigating these impacts is crucial for responsible and sustainable maritime infrastructure development. This section details the potential environmental consequences of slipway activities and explores methods for minimizing their ecological footprint.
Slipway operations present several environmental challenges. The construction process can lead to habitat disruption and soil erosion, particularly in sensitive coastal ecosystems. Furthermore, the use of heavy machinery and the potential for spills of fuel, oil, and other hazardous materials pose risks of water and soil pollution. The introduction of invasive species through vessel hulls or ballast water is another concern. Finally, noise pollution from machinery can disturb marine life.
Pollution Control Measures
Minimizing pollution is paramount. Effective waste management systems are essential, including the segregation, collection, and proper disposal of hazardous and non-hazardous wastes generated during construction and operation. This includes the careful handling of paints, solvents, and other chemicals. Regular maintenance and inspection of equipment can prevent leaks and spills. Water treatment systems, such as oil-water separators and filtration units, can significantly reduce the discharge of pollutants into the surrounding water bodies. For example, a well-designed system might incorporate a multi-stage filtration process to remove sediment, oil, and other contaminants before releasing treated water back into the environment. Regular monitoring of water quality parameters, such as turbidity, oil and grease content, and heavy metal concentrations, is crucial to assess the effectiveness of these measures.
Habitat Protection and Restoration
Protecting and restoring habitats impacted by slipway construction is a key aspect of environmental responsibility. Careful site selection, avoiding sensitive areas like seagrass beds and coral reefs, is the first step. Minimizing the footprint of the slipway through optimized design can also reduce habitat disturbance. Where habitat loss is unavoidable, mitigation measures such as habitat creation or restoration projects in nearby areas should be implemented. For instance, creating artificial reefs or restoring damaged wetlands can compensate for habitat loss. These projects often involve collaboration with environmental agencies and experts to ensure effectiveness.
Environmentally Friendly Slipway Design
An environmentally friendly slipway system incorporates sustainable materials and practices throughout its lifecycle. The use of recycled or locally sourced materials reduces the carbon footprint associated with transportation and manufacturing. Sustainable timber, for example, can be a viable alternative to concrete in certain applications. The design should minimize the use of energy and water. For example, incorporating renewable energy sources like solar panels to power lighting and machinery can significantly reduce energy consumption. Furthermore, rainwater harvesting and greywater recycling systems can reduce water usage. A well-designed drainage system prevents runoff and minimizes soil erosion. The incorporation of green infrastructure, such as vegetated roofs and walls, can enhance biodiversity and reduce stormwater runoff. Finally, the design should prioritize ease of maintenance and cleaning to prevent pollution and prolong the lifespan of the slipway. A slipway designed with these principles in mind represents a significant advancement in sustainable maritime infrastructure.
Slipway Economics and Cost Analysis
The economic feasibility of a slipway project hinges on a careful assessment of both capital expenditure and ongoing operational costs. This analysis must consider the slipway’s size, type, location, and intended use to accurately predict profitability and return on investment. Factors such as material costs, labor, and maintenance requirements significantly impact the overall cost-effectiveness.
Slipway construction and maintenance costs vary considerably depending on several key factors. A detailed breakdown allows for informed decision-making and helps identify potential cost-saving measures.
Cost Breakdown for a Concrete Slipway
Let’s consider a medium-sized concrete slipway, approximately 50 meters long and capable of handling vessels up to 50 tons. The initial investment would include costs associated with site preparation (land acquisition, leveling, and drainage), foundation work (reinforced concrete), the construction of the slipway itself (including ramps, supports, and any necessary retaining walls), and the installation of any auxiliary equipment such as winches or lifting mechanisms. Material costs for concrete, steel reinforcement, and other building materials would be substantial. Labor costs, including skilled tradespeople and project management, will also represent a significant portion of the overall budget. Contingency funds for unforeseen expenses are crucial. A rough estimate for such a project, depending on location and prevailing labor and material costs, might range from $500,000 to $1,500,000. Annual maintenance costs, including regular inspections, minor repairs, and periodic major overhauls, might range from $10,000 to $50,000, depending on environmental conditions and usage intensity.
Economic Viability of Different Slipway Designs, Slipways wiki technology
Comparing the economic viability of different slipway designs (e.g., concrete, timber, or steel) requires a comprehensive lifecycle cost analysis. While initial investment costs might vary significantly – timber slipways are generally cheaper to construct than concrete ones, for example – long-term maintenance and lifespan considerations are critical. Concrete slipways, while having higher initial costs, often boast a much longer lifespan and require less frequent maintenance than timber structures, potentially offsetting the higher upfront investment over the long term. Steel slipways offer a middle ground, but corrosion protection adds to both initial and ongoing costs. The optimal choice depends on factors like the anticipated usage intensity, the local climate, and the availability of skilled labor for different construction types.
Key Factors Influencing Slipway Cost-Effectiveness
Several key factors significantly influence the overall cost-effectiveness of slipway systems. These include:
- Initial construction costs: This encompasses material costs, labor, site preparation, and permits.
- Maintenance and repair costs: Regular inspections, repairs, and periodic overhauls are essential for ensuring the slipway’s longevity and safety.
- Lifespan: The expected lifespan of the slipway directly impacts the overall cost per year of operation.
- Environmental factors: Exposure to harsh weather conditions can accelerate deterioration and increase maintenance costs.
- Slipway usage intensity: Higher usage intensity may lead to increased wear and tear, requiring more frequent maintenance.
- Location and accessibility: Site accessibility can influence both construction and maintenance costs.
- Local labor and material costs: Regional variations in these costs can significantly affect the overall budget.
Effective cost management necessitates a detailed assessment of all these factors during the planning phase.
Slipway Safety Regulations and Standards
Safe slipway operation requires adherence to a comprehensive set of regulations and industry standards designed to minimize risks to personnel and equipment. These regulations vary depending on location and governing bodies, but common themes emphasize risk assessment, preventative maintenance, and robust operational procedures. Failure to comply can result in serious accidents, environmental damage, and legal repercussions.
Slipway safety is governed by a complex interplay of national and international regulations, alongside industry best practices. These regulations often address specific hazards associated with slipway operations, including those related to heavy lifting, confined spaces, electrical hazards, and the inherent risks of working near water. Compliance is crucial for ensuring a safe working environment and avoiding costly incidents.
Relevant Safety Regulations and Industry Standards
Numerous organizations contribute to slipway safety standards. These include national maritime authorities (e.g., the US Coast Guard, the UK Maritime and Coastguard Agency), international bodies like the International Maritime Organization (IMO), and industry associations specializing in marine engineering and construction. Specific regulations may cover aspects such as load capacity calculations, structural integrity inspections, emergency response plans, and personal protective equipment (PPE) requirements. These standards often incorporate risk assessment methodologies, requiring operators to identify and mitigate potential hazards before commencing any operation. For instance, a standard might dictate the frequency of inspections for critical components like the winch system or the slipway structure itself, specifying the criteria for acceptable wear and tear.
Safety Procedures During Vessel Launching and Hauling
Vessel launching and hauling are inherently high-risk operations. Detailed safety procedures are essential to mitigate these risks. These procedures typically include pre-operation checks of all equipment (winches, cradle, blocking systems, etc.), thorough inspections of the vessel and its securing points, clear communication protocols among the crew, and designated safety personnel overseeing the entire process. Emergency shutdown mechanisms should be readily accessible and clearly marked. Furthermore, environmental considerations, such as preventing oil spills or debris entering the water, should be integrated into the procedures. For example, a pre-launch checklist might involve verifying the integrity of the vessel’s hull, ensuring adequate lubrication of moving parts, and confirming the proper positioning of the launching cradle.
Comprehensive Safety Training Program for Slipway Operators and Maintenance Personnel
A comprehensive safety training program is paramount for ensuring safe slipway operations. This program should cover theoretical knowledge of safety regulations and practical, hands-on training. The training should include hazard identification and risk assessment techniques, safe operating procedures for all equipment, emergency response protocols, and the proper use of PPE. Regular refresher training and competency assessments are crucial to maintain high safety standards. The program should be tailored to the specific tasks performed by each individual, encompassing both theoretical and practical components. For example, winch operators would receive specialized training on winch operation, maintenance, and troubleshooting, while maintenance personnel would receive training on structural inspections and preventative maintenance techniques. Regular drills simulating emergency situations, such as winch failures or sudden vessel movements, would reinforce the practical aspects of the training. The program should also emphasize the importance of reporting near misses and accidents to foster a culture of continuous improvement in safety practices.
Case Studies of Notable Slipways
This section examines three diverse slipways, showcasing the range of design considerations and operational approaches employed in the industry. These case studies highlight successful implementations and the unique challenges overcome in different contexts. Understanding these examples provides valuable insights into best practices and potential pitfalls.
The Grand Bahama Shipyard Slipway
Located in Freeport, Grand Bahama, this slipway is a significant example of a large-scale facility designed to accommodate very large vessels. Its notable features include a substantial lifting capacity, capable of handling cruise ships and large cargo vessels. The slipway utilizes a sophisticated hydraulic system for launching and hauling vessels, minimizing the time and effort required for these operations. Its construction involved significant engineering challenges due to the soft, sandy soil conditions of the location. Extensive ground improvement techniques were implemented to ensure the structural integrity and stability of the slipway. The slipway’s design also incorporates environmental considerations, including measures to minimize water pollution and sediment runoff during operations. Regular maintenance and inspections are crucial for the safe and efficient operation of this substantial infrastructure.
The Port of San Diego Slipway
This slipway, situated within the Port of San Diego, California, is characterized by its adaptability to a variety of vessel types, from smaller recreational boats to larger commercial fishing vessels. Its design incorporates a modular system allowing for adjustments to accommodate differing vessel sizes and weights. This flexibility enhances the operational efficiency of the facility and maximizes its utilization. The slipway’s location within a busy port environment presents unique challenges related to navigation and safety. Strict operational protocols and safety measures are in place to mitigate risks associated with the high volume of marine traffic. The slipway also incorporates sustainable practices, such as rainwater harvesting and energy-efficient lighting, reflecting a commitment to environmental responsibility.
The Cammell Laird Slipway (Birkenhead)
The Cammell Laird slipway in Birkenhead, England, represents a historical example of a traditional slipway, demonstrating the evolution of slipway technology. While modernized over time, it retains aspects of its original design. Its long history has involved the launching of numerous vessels, ranging from smaller naval ships to larger commercial vessels. The slipway’s design incorporates a gravity-assisted launching system, which, while requiring careful management, minimizes reliance on extensive mechanical systems. The slipway’s location and operational history highlight the challenges of maintaining and adapting older infrastructure while meeting contemporary safety and environmental standards. Recent upgrades have focused on enhancing safety features and improving operational efficiency.
Name | Location | Vessel Type | Notable Features |
---|---|---|---|
Grand Bahama Shipyard Slipway | Freeport, Grand Bahama | Cruise ships, Large Cargo Vessels | High lifting capacity, sophisticated hydraulic system, extensive ground improvement techniques |
Port of San Diego Slipway | San Diego, California | Recreational boats, Commercial fishing vessels | Modular design, adaptability to various vessel sizes, sustainable practices |
Cammell Laird Slipway | Birkenhead, England | Naval ships, Commercial vessels | Gravity-assisted launching, historical significance, recent modernization |
Future Trends in Slipway Technology
The field of slipway technology is poised for significant advancements driven by the increasing demand for efficiency, safety, and environmental responsibility in the maritime industry. Emerging technologies offer the potential to revolutionize slipway design, operation, and maintenance, leading to faster turnaround times, reduced operational costs, and a minimized environmental footprint. This section explores some of the key future trends shaping the evolution of slipway technology.
The integration of advanced technologies like robotics, artificial intelligence (AI), and advanced materials will fundamentally alter the way slipways are designed, built, and operated. These advancements promise to enhance efficiency, improve safety protocols, and minimize the environmental impact of slipway operations. The anticipated benefits range from optimized vessel handling to reduced energy consumption and improved maintenance predictability.
Robotics and Automation in Slipway Operations
The incorporation of robotics will streamline various aspects of slipway operations. Automated guided vehicles (AGVs) could be employed to transport vessels across the slipway, ensuring precise positioning and reducing the risk of human error. Robotic arms could assist with tasks such as cleaning, painting, and minor repairs, minimizing the need for manual labor in potentially hazardous environments. Furthermore, advanced sensor systems integrated with robotic systems could provide real-time monitoring of vessel position and stability, enhancing safety and efficiency. For instance, a shipyard could implement a system where robots autonomously perform hull cleaning and inspection, reducing downtime and improving the accuracy of maintenance assessments.
AI-Driven Predictive Maintenance and Optimization
AI algorithms can analyze data from various sensors deployed across the slipway to predict potential maintenance needs and optimize operational parameters. This predictive maintenance approach reduces downtime by anticipating equipment failures and scheduling maintenance proactively. AI can also optimize the slipway’s operational schedule, considering factors such as tidal patterns, weather conditions, and vessel availability, to maximize efficiency and minimize delays. Consider a scenario where AI analyzes historical data on slipway usage, weather patterns, and equipment performance to predict potential breakdowns and optimize the scheduling of maintenance activities, minimizing downtime and ensuring the smooth operation of the slipway.
Futuristic Slipway Design: A Conceptual Illustration
Imagine a futuristic slipway constructed from advanced composite materials, offering superior strength-to-weight ratios and enhanced durability compared to traditional concrete or steel structures. This slipway would be equipped with a fully automated, robotic vessel handling system. The system would utilize a network of sensors and AI-powered control systems to precisely position and secure vessels on the slipway, minimizing the risk of damage. Integrated into the slipway structure would be a system for capturing and reusing rainwater for cleaning and other operational needs, reducing water consumption. The slipway would also feature a solar panel array to generate renewable energy, minimizing its carbon footprint. The entire system would be monitored remotely via a sophisticated control room, allowing for real-time supervision and optimization of operations. The slipway’s surface would incorporate self-healing materials, minimizing the need for frequent repairs and extending its lifespan. The vessel handling system would employ magnetic levitation technology, allowing for smooth, precise movement of vessels, reducing wear and tear on both the vessels and the slipway itself. This design would showcase a seamless integration of advanced materials, robotics, AI, and sustainable energy solutions, creating a highly efficient, safe, and environmentally friendly slipway system.
Concluding Remarks
Understanding slipway technology is paramount for the safe and efficient operation of ports and harbors worldwide. This guide has provided a detailed overview, from historical context to future trends, emphasizing the importance of sustainable practices and rigorous safety standards. By integrating technological advancements and adhering to best practices, we can ensure the continued development of efficient, environmentally responsible, and safe slipway systems for years to come.
Slipway wiki technology, focusing on collaborative knowledge management for maritime infrastructure, can benefit from advancements in semiconductor manufacturing. Understanding the precision engineering involved in slipway construction is enhanced by considering companies like axcelis technologies , whose expertise in ion implantation contributes to the miniaturization and precision found in modern sensors and control systems used in advanced slipway operations.
This connection highlights the surprising intersection between seemingly disparate fields of technology.
Slipways wiki technology, focusing on collaborative knowledge management for maritime infrastructure, often requires robust backend systems. The development of such systems can benefit from expertise in scalable solutions, such as that offered by e universe technologies llc , whose experience could significantly improve the functionality and efficiency of a slipways wiki. This ultimately leads to a more effective and user-friendly platform for sharing crucial information about slipway operations and maintenance.