Element materials technology sets the stage for this exploration, offering a comprehensive overview of the field. We will delve into the definition, types, applications, and future trends of element materials, examining their crucial role in shaping modern technology and addressing both their benefits and potential drawbacks. This discussion will cover a wide range of materials, from traditional metals and ceramics to cutting-edge composites and nanomaterials, highlighting their unique properties and diverse applications across various industries.
From the historical development of these materials to the latest advancements in synthesis and characterization techniques, we will explore the scientific principles underpinning their performance and explore the ethical and environmental considerations associated with their use. This examination will consider both the economic impact and the sustainable practices required for responsible innovation in this critical field.
Defining “Element Materials Technology”
Element materials technology is a specialized field within materials science and engineering that focuses on the understanding, design, and application of materials based on individual elements and their inherent properties. It delves into the atomic-level characteristics of elements to tailor their behavior for specific technological needs, extending beyond simple alloying to encompass sophisticated techniques for manipulating elemental properties. This includes considerations of their electronic structure, crystallographic arrangements, and interactions with other elements or environments. The field encompasses both fundamental research and practical applications.
Element materials technology distinguishes itself from other materials science branches by its emphasis on the intrinsic properties of individual elements as the primary building blocks. Unlike fields that focus on composite materials or alloys where the properties are a blend of constituent elements, this field aims to exploit and enhance the unique characteristics of each element. For example, the study of graphene, a single layer of carbon atoms, falls under this umbrella, as it leverages the exceptional properties of the carbon element itself rather than relying on a combination of elements. This focus on elemental purity and precise control over atomic arrangements leads to the creation of advanced materials with exceptional performance.
The Historical Development of Element Materials Technology
The historical development of element materials technology is intrinsically linked to the advancements in our understanding of atomic structure and the ability to manipulate materials at the atomic level. Early stages were largely empirical, with discoveries driven by trial and error and the observation of material properties. The development of techniques like X-ray crystallography in the early 20th century revolutionized the field, allowing for detailed analysis of atomic arrangements and their correlation with material properties. Subsequent breakthroughs in materials synthesis, such as chemical vapor deposition (CVD) and molecular beam epitaxy (MBE), enabled the precise control over the growth of thin films and nanostructures, pushing the boundaries of what could be achieved with elemental materials. The invention of the scanning tunneling microscope (STM) and atomic force microscope (AFM) further advanced the field by allowing direct visualization and manipulation of individual atoms. These tools have enabled the creation of novel materials with precisely controlled properties, such as tailored electronic and optical properties in semiconductor materials. The ongoing quest for higher performance in electronics, energy storage, and other technologies continues to drive innovation in element materials technology.
Types of Element Materials
Element materials form the bedrock of modern technology, their diverse properties shaping the functionalities and capabilities of countless devices and structures. Understanding the characteristics of different material types is crucial for selecting the optimal material for a specific application, balancing performance requirements with cost and availability considerations. This section will explore the key categories of element materials—metals, ceramics, polymers, and composites—examining their individual properties and comparing their strengths and weaknesses.
Metals
Metals are characterized by their high electrical and thermal conductivity, ductility (ability to be drawn into wires), and malleability (ability to be hammered into sheets). Their crystalline structure contributes to these properties. Examples include iron, aluminum, copper, and titanium. Iron, a key component of steel, exhibits high strength but is susceptible to corrosion. Aluminum offers a good strength-to-weight ratio and excellent corrosion resistance, making it ideal for aerospace applications. Copper’s exceptional electrical conductivity makes it indispensable in wiring and electronics. Titanium boasts high strength and excellent biocompatibility, finding use in medical implants. However, metals can be relatively expensive and may require specialized processing techniques.
Ceramics
Ceramics are inorganic, non-metallic materials formed from compounds of metallic and non-metallic elements. They are typically hard, brittle, and possess high melting points. Their strong ionic or covalent bonds contribute to their high strength at high temperatures and excellent chemical resistance. Examples include alumina (Al₂O₃), zirconia (ZrO₂), and silicon carbide (SiC). Alumina finds applications in high-temperature applications and as an abrasive. Zirconia’s high strength and toughness make it suitable for dental implants and cutting tools. Silicon carbide’s exceptional hardness makes it a valuable material for cutting tools and wear-resistant components. However, ceramics are brittle and prone to fracture under stress.
Polymers
Polymers are large molecules composed of repeating structural units called monomers. They are typically lightweight, flexible, and possess good insulating properties. Their diverse chemical structures lead to a wide range of properties, from flexible plastics to high-strength fibers. Examples include polyethylene (PE), polypropylene (PP), and polytetrafluoroethylene (PTFE, Teflon). Polyethylene is widely used in plastic bags and films due to its low cost and flexibility. Polypropylene finds use in various applications, including packaging and automotive parts, owing to its strength and chemical resistance. PTFE’s exceptional chemical inertness and low friction coefficient make it suitable for non-stick coatings and high-performance seals. However, polymers generally have lower strength and thermal stability compared to metals and ceramics.
Composites
Composites are materials composed of two or more constituent materials with significantly different properties. The combination of these materials results in a material with enhanced properties not found in the individual components. This synergistic effect allows for the design of materials with tailored properties to meet specific application needs. Examples include fiberglass (glass fibers in a polymer matrix), carbon fiber reinforced polymers (CFRP), and concrete (aggregate and cement). Fiberglass is lightweight and strong, used extensively in boats and sporting goods. CFRP boasts exceptional strength-to-weight ratio, making it ideal for aerospace and automotive applications. Concrete’s high compressive strength makes it a ubiquitous construction material. The properties of composites are highly dependent on the properties of their constituents and the interfacial bonding between them.
Comparison of Material Properties
The following table compares the mechanical, electrical, and thermal properties of five common element materials:
Material | Mechanical Properties (Tensile Strength, MPa) | Electrical Conductivity (MS/m) | Thermal Conductivity (W/m·K) |
---|---|---|---|
Steel | 500-1500 | 0.1-0.2 | 45-50 |
Aluminum | 70-700 | 37 | 200-240 |
Alumina (Al₂O₃) | 300-400 | ~10⁻¹⁴ | 25-40 |
Polyethylene (PE) | 10-30 | ~10⁻¹⁵ | 0.3-0.5 |
Carbon Fiber Reinforced Polymer (CFRP) | 700-2000+ | ~10⁻¹⁰ | 10-200 (depending on fiber orientation and volume fraction) |
Applications of Element Materials Technology
Element materials technology, encompassing the study, design, and application of materials at the atomic and molecular level, has profoundly impacted numerous industries. Its influence stems from the ability to tailor material properties – strength, conductivity, reactivity – with unprecedented precision, leading to innovations across diverse sectors. This section will explore some key applications, highlighting both established uses and emerging possibilities.
Aerospace Applications
The aerospace industry demands materials with exceptional strength-to-weight ratios, high temperature resistance, and excellent fatigue properties. Element materials technology plays a crucial role in meeting these stringent requirements. For instance, advanced alloys incorporating titanium, aluminum, and nickel are used in aircraft structures, engines, and spacecraft components. Carbon fiber reinforced polymers (CFRPs), a composite material utilizing carefully selected elements, are increasingly employed for lighter and stronger airframes, contributing to fuel efficiency and reduced emissions. The development of novel high-temperature alloys, incorporating elements like rhenium and tantalum, is pushing the boundaries of engine performance and enabling hypersonic flight.
Electronics Applications
The electronics industry relies heavily on element materials with specific electrical and thermal properties. Silicon, the cornerstone of microelectronics, is refined and manipulated at the atomic level to create increasingly powerful and efficient integrated circuits. Rare earth elements, such as neodymium and dysprosium, are essential components in permanent magnets used in various electronic devices, from hard disk drives to electric motors. The pursuit of smaller, faster, and more energy-efficient electronics drives ongoing research into new element materials, including graphene and other two-dimensional materials, which offer exceptional conductivity and potential for revolutionary advancements in computing and communication technologies.
Energy Applications
Element materials technology is vital for addressing global energy challenges. In renewable energy technologies, advanced materials are crucial. For example, silicon-based solar cells rely on precise control of elemental composition to maximize energy conversion efficiency. Similarly, the development of efficient and durable batteries for electric vehicles and energy storage systems necessitates the exploration of new electrode materials and electrolytes, often incorporating elements like lithium, cobalt, and manganese. Nuclear energy also benefits from advanced materials that can withstand extreme conditions and resist radiation damage, often employing specialized alloys with carefully selected elements to maintain structural integrity.
Innovative Applications in Emerging Technologies
The unique properties of element materials are being harnessed in emerging technologies. Nanotechnology utilizes the manipulation of elements at the nanoscale to create materials with enhanced properties. For instance, nanoparticles of silver exhibit potent antimicrobial properties, finding applications in medical devices and wound dressings. In biotechnology, element materials are used in biosensors and drug delivery systems. For example, gold nanoparticles are frequently used as contrast agents in medical imaging due to their unique optical properties. The development of biocompatible materials, often incorporating elements like titanium and zirconium, is crucial for implants and prosthetics.
Hypothetical Scenario: A Novel Element Material in Energy Storage
Imagine a newly synthesized element material, tentatively named “Element X,” exhibiting exceptional energy density and charge-discharge rates far exceeding those of current lithium-ion batteries. This hypothetical material, possessing a unique crystal structure and electron configuration, allows for highly efficient ion transport and minimal energy loss during charging and discharging cycles. Element X could revolutionize electric vehicle technology, enabling longer driving ranges and significantly shorter charging times. Its impact would extend beyond transportation, offering a more efficient and cost-effective solution for grid-scale energy storage, improving the reliability and integration of renewable energy sources. This hypothetical breakthrough would necessitate new manufacturing processes and infrastructure, but its potential economic and environmental benefits are enormous, mirroring the impact of silicon in microelectronics.
Material Synthesis and Processing
The creation of element materials, whether pure elements or alloys, involves a series of crucial synthesis and processing steps that directly influence the final material’s properties and performance. The selection of appropriate techniques depends heavily on the desired properties, the element’s inherent characteristics, and economic considerations. Understanding these processes is paramount to controlling the quality and consistency of the final product.
The synthesis and processing of element materials encompass a range of techniques, each with its own advantages and limitations. These techniques are often tailored to the specific material being produced, with careful consideration given to purity, cost-effectiveness, and the desired microstructure. Control over processing parameters is critical for achieving the targeted properties, making precise control and monitoring essential throughout the entire process.
Casting
Casting involves melting a material and pouring it into a mold, allowing it to solidify into the desired shape. This is a versatile technique suitable for various element materials, including metals and some ceramics. Different casting methods exist, such as die casting (using metal molds for high-volume production of complex shapes), investment casting (using a wax pattern), and continuous casting (for producing long, continuous lengths of material). The cooling rate during solidification significantly impacts the resulting microstructure and mechanical properties. Faster cooling rates generally lead to finer grain sizes, resulting in increased strength and hardness, while slower cooling rates can produce larger grains, potentially leading to improved ductility.
Forging
Forging involves shaping a material by applying compressive forces using hammers or presses. This process is commonly used to improve the mechanical properties of metals, particularly increasing their strength and ductility. Forging is typically performed at elevated temperatures, making the metal more malleable and easier to shape. The process can refine the grain structure, remove internal defects, and improve the material’s overall homogeneity. Different forging techniques exist, such as open-die forging (using simple flat dies) and closed-die forging (using complex shaped dies for precise geometries).
Powder Metallurgy
Powder metallurgy involves consolidating metal powders into a desired shape through pressing and sintering. This method offers several advantages, including the ability to create complex shapes with precise dimensions, utilize materials with high melting points, and produce materials with unique microstructures and compositions. The process typically begins with the production of fine metal powders, followed by blending, pressing the powder into the desired shape, and then sintering at high temperatures to bond the particles together. Controlling the powder size distribution, pressing pressure, and sintering temperature are crucial for achieving the desired density and mechanical properties.
Step-by-Step Synthesis of Copper from Copper Oxide
This procedure Artikels the synthesis of high-purity copper from copper(II) oxide using a reduction process. Precise control of temperature and the reducing agent is critical for achieving high purity. Safety precautions must be rigorously followed throughout the process.
- Equipment: Furnace capable of reaching 1000°C, crucible (e.g., alumina), weighing balance, spatula, tongs, gas cylinder (hydrogen or carbon monoxide), gas flow meter, protective eyewear, gloves, lab coat.
- Materials: Copper(II) oxide (CuO), reducing agent (hydrogen or carbon monoxide).
- Procedure:
- Weigh a precise amount of CuO and place it into the crucible.
- Place the crucible into the furnace.
- Slowly increase the furnace temperature to 800-1000°C under a controlled flow of the reducing gas (hydrogen or carbon monoxide). This will reduce the CuO to metallic copper (CuO + H2 → Cu + H2O).
- Maintain the temperature for a sufficient time to ensure complete reduction (typically 1-2 hours).
- Slowly cool the furnace to room temperature under a continued flow of the reducing gas to prevent oxidation of the copper.
- Remove the crucible and carefully extract the copper.
- Safety Precautions: Hydrogen and carbon monoxide are flammable and potentially toxic gases. Ensure adequate ventilation and use appropriate safety equipment. The furnace will reach high temperatures; avoid direct contact. Handle chemicals with care and follow proper waste disposal procedures.
Characterization Techniques
Understanding the properties of element materials is crucial for their effective application. This requires a suite of characterization techniques that probe the material’s structure at various length scales, from atomic arrangements to macroscopic features. These techniques provide critical insights into the relationship between a material’s microstructure and its overall performance.
Various techniques, broadly categorized as microscopy, spectroscopy, and diffraction, are employed to characterize the properties of element materials. Microscopy provides visual information about the material’s structure, while spectroscopy analyzes the interaction of electromagnetic radiation with the material to reveal its composition and electronic structure. Diffraction techniques utilize the scattering of waves (X-rays, electrons, or neutrons) to determine the crystallographic arrangement of atoms within the material.
Microscopy Techniques
Microscopy offers direct visualization of material microstructure, ranging from surface topography to internal features. Different microscopy techniques provide complementary information at different length scales and resolutions. For example, optical microscopy provides a relatively low-resolution image of the surface, suitable for observing large-scale features such as grain boundaries in a polycrystalline material. Scanning electron microscopy (SEM) provides higher resolution images, revealing details of surface morphology and composition using electron beams. Transmission electron microscopy (TEM), on the other hand, allows for the observation of internal microstructure at the atomic level by transmitting electrons through a thin sample.
Spectroscopy Techniques
Spectroscopy techniques analyze the interaction of electromagnetic radiation (light, X-rays, etc.) with the material to obtain information about its composition, electronic structure, and chemical bonding. X-ray photoelectron spectroscopy (XPS) provides information on the elemental composition and chemical states of atoms at the surface of a material. Energy-dispersive X-ray spectroscopy (EDS), often coupled with SEM, provides elemental mapping and composition analysis. UV-Vis spectroscopy measures the absorption and transmission of light, providing insights into electronic transitions and band gaps in materials.
Diffraction Techniques
Diffraction techniques utilize the constructive and destructive interference of waves (X-rays, electrons, or neutrons) scattered by the periodic arrangement of atoms in a crystal to determine its crystal structure. X-ray diffraction (XRD) is widely used to identify phases, determine crystallite size, and measure strain in crystalline materials. Electron diffraction, often used in conjunction with TEM, provides information on the crystal structure at a nanoscale. Neutron diffraction is particularly useful for studying materials with light elements or magnetic structures because neutrons interact differently with atoms compared to X-rays.
Comparison of Characterization Techniques
The choice of characterization technique depends on the specific information needed and the nature of the material being studied. Each technique has its own advantages and limitations.
Technique | Advantages | Limitations | Example Application |
---|---|---|---|
SEM | High resolution imaging of surface morphology, elemental mapping (with EDS) | Surface sensitive, requires conductive sample for optimal imaging | Analyzing the surface roughness of a thin film |
XRD | Identifies crystalline phases, determines crystallite size and strain | Requires crystalline material, may not be sensitive to amorphous phases | Determining the phase composition of a metal alloy |
XPS | Provides information on elemental composition and chemical states at the surface | Surface sensitive, requires ultra-high vacuum | Analyzing the oxidation state of a metal oxide |
Material Performance and Degradation
The performance and lifespan of element materials are critically influenced by their interaction with the operating environment. Understanding the mechanisms of degradation is crucial for designing reliable and long-lasting components and systems. This section explores the key factors affecting material performance and the strategies employed to mitigate degradation.
Understanding the factors that influence the performance and degradation of element materials is paramount in ensuring the longevity and reliability of engineered systems. Environmental conditions, inherent material properties, and processing techniques all play significant roles in determining a material’s service life. Degradation mechanisms, such as corrosion, creep, and fatigue, can lead to catastrophic failure if not properly addressed.
Environmental Factors Affecting Material Performance
Temperature, corrosive environments, and radiation exposure significantly impact the performance and degradation of element materials. Elevated temperatures can accelerate diffusion processes, leading to creep (time-dependent deformation under constant stress) and accelerated oxidation. Corrosive environments, such as acidic or saline solutions, can initiate chemical reactions that dissolve or weaken the material’s structure. Similarly, exposure to ionizing radiation can create defects within the material’s crystal lattice, leading to embrittlement and reduced strength. For instance, high-temperature alloys used in gas turbines experience creep and oxidation at elevated operating temperatures, requiring careful material selection and protective coatings. Stainless steels, commonly used in marine applications, are susceptible to pitting corrosion in chloride-containing environments, necessitating the use of corrosion inhibitors or more resistant alloys. Nuclear reactor components must withstand high levels of radiation, necessitating the use of radiation-resistant materials like zirconium alloys.
Mechanisms of Material Degradation and Failure
Material degradation often involves a complex interplay of physical and chemical processes. Corrosion, for example, can be electrochemical (involving electron transfer) or chemical (direct reaction with the environment). Fatigue failure occurs due to cyclic loading, leading to the propagation of cracks and eventual fracture. Creep, as mentioned previously, is a time-dependent deformation under constant stress, often occurring at elevated temperatures. Fracture mechanics provides a framework for understanding crack initiation and propagation, enabling the prediction of material lifespan under various loading conditions. For instance, a fatigue crack in a metal component might initiate at a stress concentration (e.g., a sharp corner) and propagate until the remaining cross-section can no longer support the applied load, resulting in sudden fracture.
Strategies for Enhancing Material Durability and Lifespan
Several strategies can be employed to enhance the durability and lifespan of element materials. These include material selection based on the specific application and operating environment, surface modification techniques (such as coatings or surface treatments), and the use of protective barriers. Alloying can improve the material’s resistance to corrosion, creep, and oxidation. Protective coatings, like thermal barrier coatings (TBCs) for high-temperature applications, provide a barrier against harsh environments. Controlled processing techniques, such as heat treatments, can optimize the material’s microstructure and mechanical properties. Regular inspection and maintenance are also critical for preventing premature failure. For example, the addition of chromium to steel significantly improves its corrosion resistance, making stainless steel suitable for various applications. The application of a ceramic coating on a metal component can provide thermal insulation and protect against oxidation at high temperatures.
Emerging Trends in Element Materials Technology
The field of element materials technology is experiencing a period of rapid advancement, driven by the need for materials with enhanced properties and functionalities to address global challenges in energy, electronics, and healthcare. This evolution is fueled by innovative synthesis techniques, sophisticated characterization methods, and the increasing power of computational tools. These trends are reshaping our ability to design and manufacture materials with unprecedented precision and performance.
Several key trends are defining the future of element materials technology. These advancements are not isolated events but rather interconnected developments that are synergistically pushing the boundaries of what’s possible.
Development of Novel Materials with Enhanced Properties
The pursuit of materials with superior strength, lighter weight, improved conductivity, or enhanced resistance to extreme environments is a central theme. For instance, the development of high-entropy alloys (HEAs), composed of five or more principal elements in near-equiatomic ratios, is yielding materials with exceptional properties such as high strength and corrosion resistance. These alloys demonstrate a significant improvement over traditional alloys due to their unique microstructure and complex interactions between constituent elements. Another example is the exploration of two-dimensional (2D) materials like graphene and transition metal dichalcogenides (TMDs), which exhibit remarkable electronic and optical properties, paving the way for advancements in flexible electronics and optoelectronics.
Advanced Computational Modeling and Simulation in Materials Design
Computational methods, including density functional theory (DFT) and molecular dynamics (MD), are playing an increasingly crucial role in materials design. These techniques allow researchers to predict the properties of materials before they are synthesized, significantly reducing the time and cost associated with experimental trial and error. For example, DFT calculations can accurately predict the electronic band structure of new materials, guiding the design of semiconductors with specific optoelectronic properties. Furthermore, MD simulations can model the behavior of materials under various conditions, such as high temperature or pressure, providing valuable insights into their performance and durability. This computational approach enables the exploration of a vast design space, accelerating the discovery of novel materials with tailored characteristics.
Predictions Regarding Future Advancements and Challenges
The future of element materials technology promises continued advancements in material synthesis, characterization, and application. We can expect to see a greater emphasis on sustainable and environmentally friendly materials, driven by the growing need for responsible resource management. The integration of artificial intelligence (AI) and machine learning (ML) into materials design and discovery will further accelerate the pace of innovation, enabling the rapid identification of novel materials with desired properties. However, challenges remain, including the need for more efficient and scalable synthesis methods, the development of advanced characterization techniques to probe materials at the atomic level, and the need to address the ethical implications of advanced materials technologies. For instance, the widespread adoption of HEAs may depend on overcoming challenges related to cost-effective production and ensuring consistent material quality. Similarly, the full potential of 2D materials will require overcoming challenges related to their scalability and integration into existing technologies. The development of robust predictive models for material degradation and failure will be crucial for ensuring the reliability and safety of advanced materials in various applications.
Sustainability and Environmental Impact
The element materials industry, while crucial for technological advancement, faces significant challenges regarding its environmental footprint. The extraction, processing, and disposal of these materials often involve energy-intensive processes and generate substantial waste, impacting air and water quality, and contributing to climate change. A comprehensive understanding of these impacts and the adoption of sustainable practices are vital for ensuring the long-term viability of the industry and protecting the environment.
The environmental impact of element materials spans their entire lifecycle. Mining operations, for example, can lead to habitat destruction, soil erosion, and water contamination from chemical runoff. The refining and processing of raw materials often require high temperatures and the use of harsh chemicals, releasing greenhouse gases and other pollutants into the atmosphere. Finally, the disposal of end-of-life products containing these materials can lead to landfill accumulation and potential leaching of harmful substances into the environment. Specific impacts vary greatly depending on the material in question; for instance, the rare earth element mining process is known for its particularly high environmental cost due to the complex extraction methods and the generation of significant waste.
Environmental Impacts of Element Material Extraction
Mining and extraction of element materials often involve significant land disturbance, leading to habitat loss and biodiversity reduction. The process frequently generates large quantities of waste rock and tailings, which can contaminate water sources with heavy metals and other toxic substances. Furthermore, energy consumption during mining and transportation of materials contributes significantly to greenhouse gas emissions. For example, the extraction of lithium for batteries, a crucial element in many modern technologies, has raised concerns about water depletion and the creation of vast tailings ponds in regions with limited water resources.
Sustainable Practices in Element Materials Production
The adoption of sustainable practices is crucial to mitigating the environmental impact of element materials. This includes implementing cleaner production technologies, such as improved energy efficiency in processing plants and the development of closed-loop systems to minimize waste generation. The use of renewable energy sources in mining and processing operations can significantly reduce greenhouse gas emissions. Furthermore, responsible sourcing of materials, ensuring compliance with environmental regulations, and promoting transparency throughout the supply chain are vital steps towards sustainability. Examples of such practices include the use of hydrometallurgy (water-based extraction) instead of pyrometallurgy (high-temperature methods) in some rare earth element extraction processes, which reduces energy consumption and greenhouse gas emissions.
Recycling and Reuse of Element Materials
Recycling and reuse play a critical role in minimizing the environmental impact of element materials. By recovering valuable materials from end-of-life products and reintroducing them into the production cycle, we can reduce the demand for newly mined resources, conserving natural resources and minimizing waste generation. Efficient recycling processes require the development of advanced separation and purification technologies to recover valuable elements from complex mixtures. For example, the recycling of lithium-ion batteries is gaining increasing attention as a means of recovering valuable metals like lithium, cobalt, and nickel, reducing the reliance on virgin materials and mitigating the environmental burden associated with their extraction. This also includes initiatives focused on designing products for easier disassembly and material recovery at the end of their life cycle, a concept known as Design for Recycling (DfR).
Economic Aspects of Element Materials
Element materials, encompassing a vast range of substances from rare earth elements to advanced alloys, play a crucial role in the global economy. Their economic significance extends across numerous sectors, influencing national competitiveness and shaping international trade dynamics. Understanding the economic aspects of these materials is critical for informed policymaking, strategic investment, and sustainable resource management.
The economic value of element materials is intrinsically linked to their properties and applications. High-performance materials, for instance, command premium prices due to their superior strength, durability, or specialized functionalities. Conversely, the abundance and ease of extraction of certain elements contribute to lower costs. This interplay between material properties, processing complexity, and market demand significantly impacts the economic landscape.
Factors Influencing Cost and Availability
Several factors intricately influence the cost and availability of element materials. Geopolitical considerations, particularly the concentration of resources in specific regions, can create supply chain vulnerabilities and price volatility. For example, the dominance of a few countries in the production of rare earth elements has led to price fluctuations and concerns about resource security. Technological advancements in extraction and processing techniques also play a significant role. Innovations that improve efficiency and reduce waste can lower production costs and increase material availability. Environmental regulations, aimed at mitigating the environmental impact of mining and processing, can add to production expenses, affecting the final cost of element materials. Finally, market demand, driven by technological advancements and industrial growth, significantly impacts prices. Increased demand for specific element materials, such as those used in renewable energy technologies, can lead to price increases.
Hypothetical Market Analysis: A Novel Superconductor
Imagine a hypothetical scenario where a new element material, designated “Element X,” is discovered. Element X exhibits exceptional superconducting properties at room temperature, surpassing the capabilities of existing materials. This breakthrough would have profound economic implications. Initially, the high cost of Element X extraction and purification would limit its applications to high-value sectors like medical imaging and advanced computing. However, as production scales up and processing techniques improve, the cost would likely decrease, enabling wider adoption in areas such as energy transmission and transportation. A market analysis might predict an initial market capitalization of $5 billion within five years, rising to $50 billion within a decade, driven by the substantial cost savings in energy transmission alone. This would be comparable to the economic impact of the lithium-ion battery market’s growth, driven by the demand for electric vehicles and energy storage solutions. This rapid growth would, however, necessitate careful management of supply chains to avoid price volatility and ensure equitable access to this transformative material. Furthermore, the development of Element X could spur innovation in related industries, leading to further economic growth and job creation.
Ethical Considerations
The development and application of element materials technology present a complex array of ethical considerations that extend beyond the purely scientific and economic realms. Responsible innovation and sustainable practices are paramount to mitigating potential negative impacts on society and the environment. This section examines key ethical dilemmas associated with the sourcing, use, and development of advanced element materials.
Ethical implications are inherent in the entire lifecycle of element materials, from extraction and processing to application and disposal. Decisions made at each stage have far-reaching consequences, impacting not only the environment but also the social and economic well-being of communities. Careful consideration must be given to ensuring fairness, transparency, and accountability throughout the entire process.
Sourcing of Conflict Minerals
The sourcing of certain element materials, particularly those used in electronics and other high-tech applications, is often associated with conflict minerals. These minerals, such as tantalum, tin, tungsten, and gold (3TG), are mined in regions affected by armed conflict, where their extraction often fuels violence and human rights abuses. The ethical challenge lies in establishing robust supply chains that ensure these materials are sourced from conflict-free regions and that workers are treated fairly and safely. Traceability systems and independent audits are crucial in addressing this challenge. For example, the implementation of the Dodd-Frank Act in the United States mandates that publicly listed companies disclose the use of conflict minerals in their products.
Environmental Impact of Extraction and Processing
The extraction and processing of many element materials can have significant environmental impacts, including habitat destruction, water pollution, and greenhouse gas emissions. For instance, the mining of rare earth elements, crucial for many advanced technologies, is known for its high environmental cost, involving the generation of large amounts of toxic waste. Ethical considerations require the adoption of environmentally sound mining practices, including the use of cleaner technologies and the implementation of effective waste management strategies. Furthermore, life cycle assessments should be conducted to evaluate the overall environmental impact of element materials throughout their entire lifecycle, from cradle to grave.
Responsible Innovation and Sustainable Practices
Responsible innovation in element materials technology necessitates a commitment to sustainability throughout the entire innovation process. This involves considering the environmental, social, and economic impacts of new materials and technologies from the initial research and development stages. A key aspect of responsible innovation is the development of sustainable alternatives to materials with high environmental or social costs. For example, research into recycling and reuse strategies for element materials is crucial for reducing the environmental impact of their production and disposal. Furthermore, the development of materials with enhanced recyclability and biodegradability is an important aspect of sustainable material design.
Potential Ethical Dilemmas in Advanced Materials Development
The development and application of advanced element materials, such as nanomaterials and metamaterials, present unique ethical challenges. The potential toxicity and unknown long-term effects of some of these materials necessitate rigorous safety testing and risk assessment before their widespread use. Furthermore, the potential for misuse of advanced materials, such as in the development of autonomous weapons systems, raises serious ethical concerns that require careful consideration and proactive measures to mitigate risks. Transparency and open dialogue among scientists, policymakers, and the public are essential for addressing these complex ethical dilemmas.
Case Studies
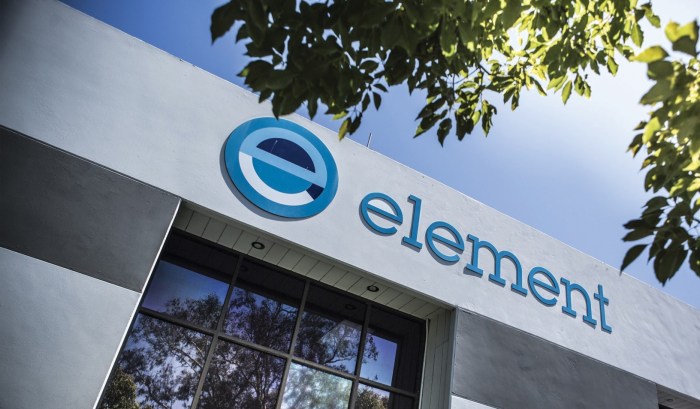
This section details successful applications of element materials technology across various industries, highlighting the materials employed, challenges overcome, and solutions implemented. The case studies demonstrate the significant impact of advanced materials on improving product performance, efficiency, and sustainability.
High-Strength Steel in Automotive Manufacturing, Element materials technology
The automotive industry consistently seeks lighter, stronger materials to improve fuel efficiency and vehicle safety. High-strength steel alloys, specifically advanced high-strength steels (AHSS), have become a cornerstone of modern vehicle design. These materials offer a superior strength-to-weight ratio compared to conventional steels.
The following points summarize a successful application of AHSS in a specific vehicle model:
- Material Used: Dual-phase (DP) and transformation-induced plasticity (TRIP) AHSS grades, exhibiting high tensile strength and excellent formability.
- Challenges Faced: Achieving complex shapes during manufacturing while maintaining consistent material properties and preventing cracking. High tooling costs associated with the increased strength of the material were also a concern.
- Solutions Implemented: Advanced forming processes like tailored blank technology, which combines different steel grades in a single component, were utilized to optimize material properties and reduce weight. Precise control of the manufacturing process, including temperature and pressure, was crucial to prevent defects. Investment in new tooling and advanced simulation techniques aided in overcoming manufacturing challenges.
- Outcome: A significant reduction in vehicle weight, leading to improved fuel economy and reduced CO2 emissions. Enhanced crash safety performance due to the higher strength of the AHSS was also achieved.
Lightweight Composites in Aerospace Engineering
The aerospace industry demands materials with exceptional strength-to-weight ratios, high stiffness, and resistance to extreme temperatures. Carbon fiber reinforced polymers (CFRPs) have emerged as a leading material choice, enabling the construction of lighter and more fuel-efficient aircraft.
The following points describe a successful implementation of CFRPs in a commercial aircraft:
- Material Used: Carbon fiber reinforced epoxy resin composites, tailored for specific structural components based on required strength and stiffness.
- Challenges Faced: High manufacturing costs, complex joining techniques, and the need for rigorous quality control to ensure structural integrity. The potential for delamination and damage tolerance also needed careful consideration.
- Solutions Implemented: Automated fiber placement (AFP) and out-of-autoclave curing techniques were employed to reduce manufacturing time and costs. Advanced joining methods, such as adhesive bonding and mechanically fastened joints, were developed to ensure strong and reliable connections between composite components. Extensive non-destructive testing (NDT) methods were implemented to detect any defects.
- Outcome: Significant weight reduction in the aircraft structure, resulting in improved fuel efficiency and reduced operating costs. Enhanced structural performance and increased passenger capacity were also achieved.
Final Thoughts
In conclusion, element materials technology is a dynamic and ever-evolving field with far-reaching implications for technological advancement and societal progress. Understanding the properties, applications, and limitations of various element materials is crucial for engineers, scientists, and policymakers alike. By embracing sustainable practices and addressing ethical considerations, we can harness the power of element materials technology to create a more innovative and sustainable future. The ongoing research and development in this field promise exciting breakthroughs and innovations in the years to come, driving further advancements across various sectors and shaping the technological landscape of tomorrow.